Last Updated on 2025-02-20 by Anze
Laser leather perforation machine and CNC leather perforation machine are two types of equipment widely used in the leather processing industry. They have significant differences in technical principles, processing effects, and scope of application. Here’s a detailed comparison of the two devices:
Technical principles
Laser leather perforation machine:
Utilizes the high energy density characteristics of the laser beam to generate high temperature on the leather surface by focusing the laser beam, causing the material to quickly vaporize, melt or reach the ignition point, thereby forming holes in the leather. The process is non-contact, with the laser beam acting directly on the material surface without physical contact.
CNC leather perforation machine:
Uses CNC technology to control mechanical movement and punches leather through preset programs and molds. It uses mechanical force to press a mold into the leather to create the desired holes. This process is physical and requires direct contact between the mold and the leather.
Processing effect
Laser leather perforation machine:
Due to the high precision and controllability of the laser beam, the laser leather perforation machine can achieve very fine hole processing. The edges of the holes are smooth, burr-free, and not easily deformed. However, laser processing may produce a certain heat-affected zone on the leather surface, causing local discoloration or hardening of the leather.
CNC leather perforation machine:
CNC leather perforation machine punches holes through a mold, so the shape and size of the hole depends on the design of the mold. Mold punching can usually achieve more uniform holes, but wear of the mold and changes in the thickness of the leather may affect the processing quality. In addition, the CNC perforation machine may produce certain mechanical stress on the leather during processing.
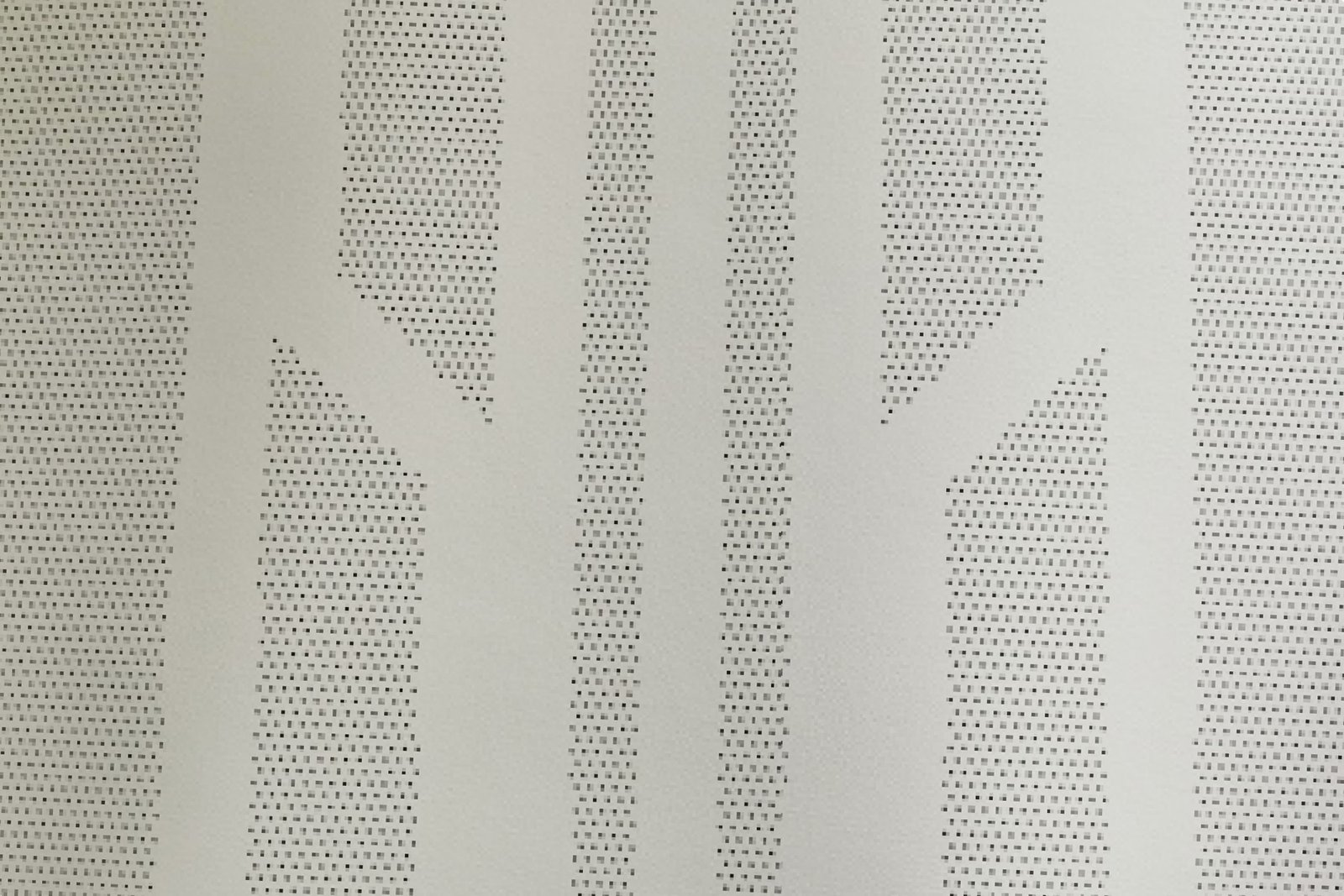
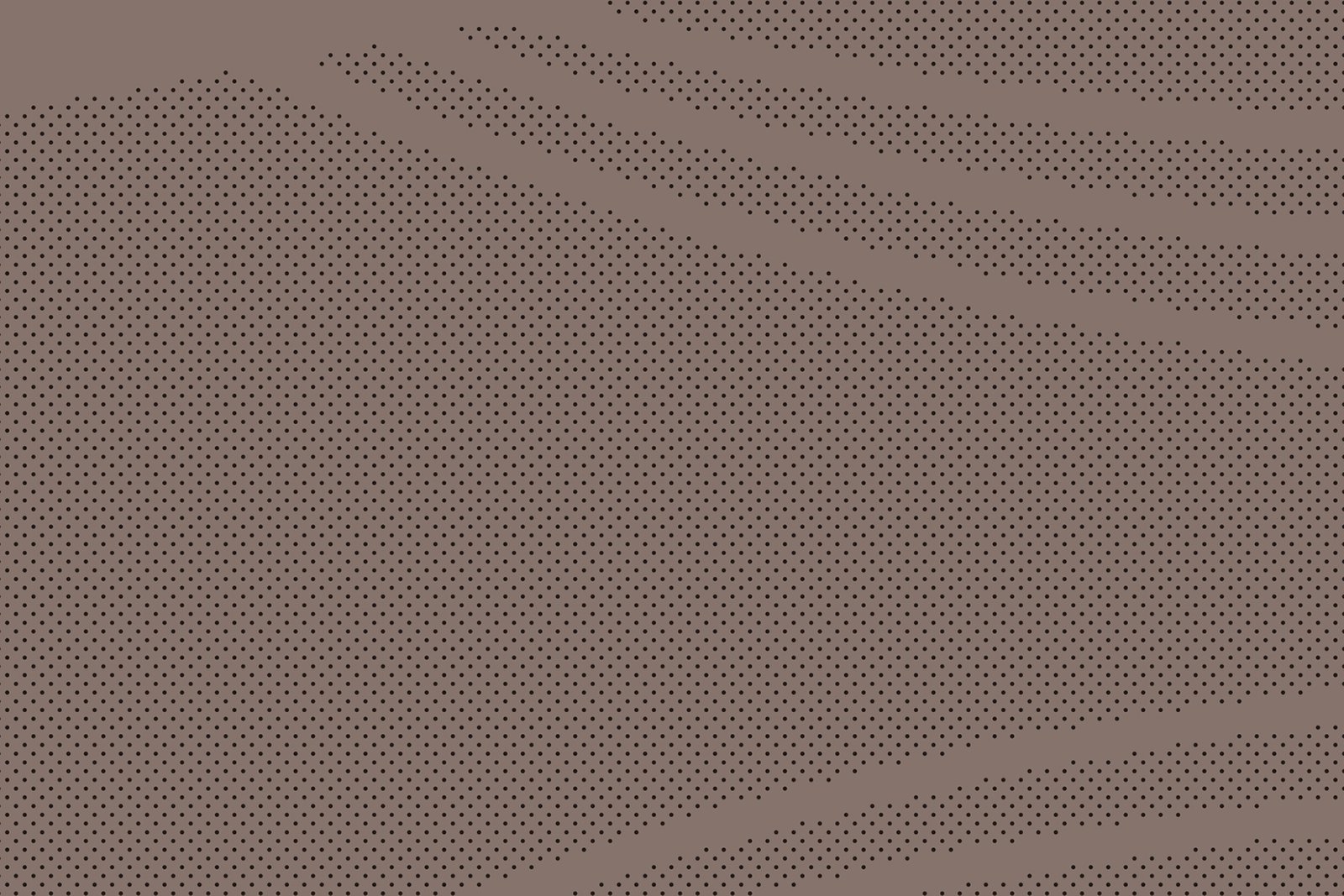
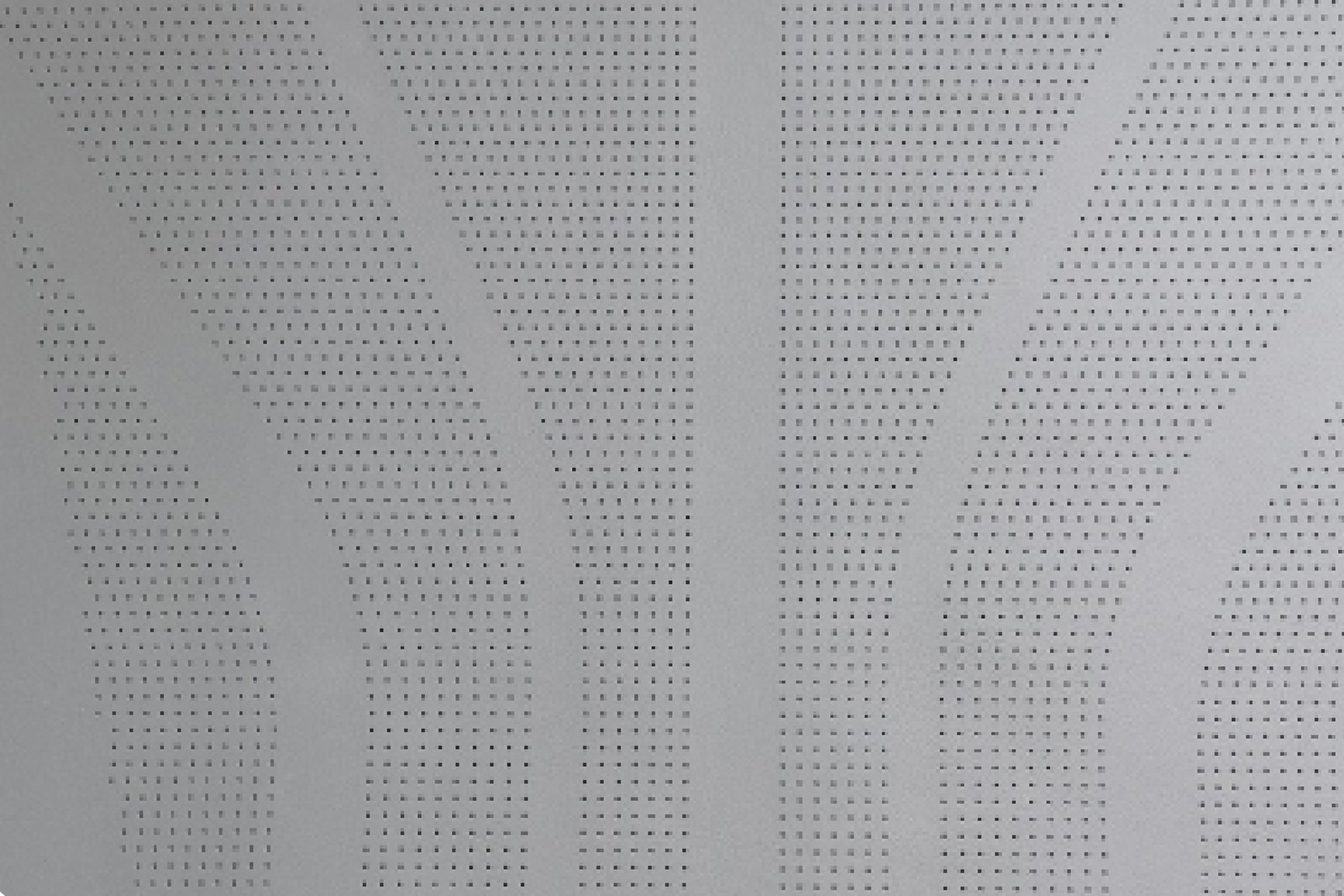
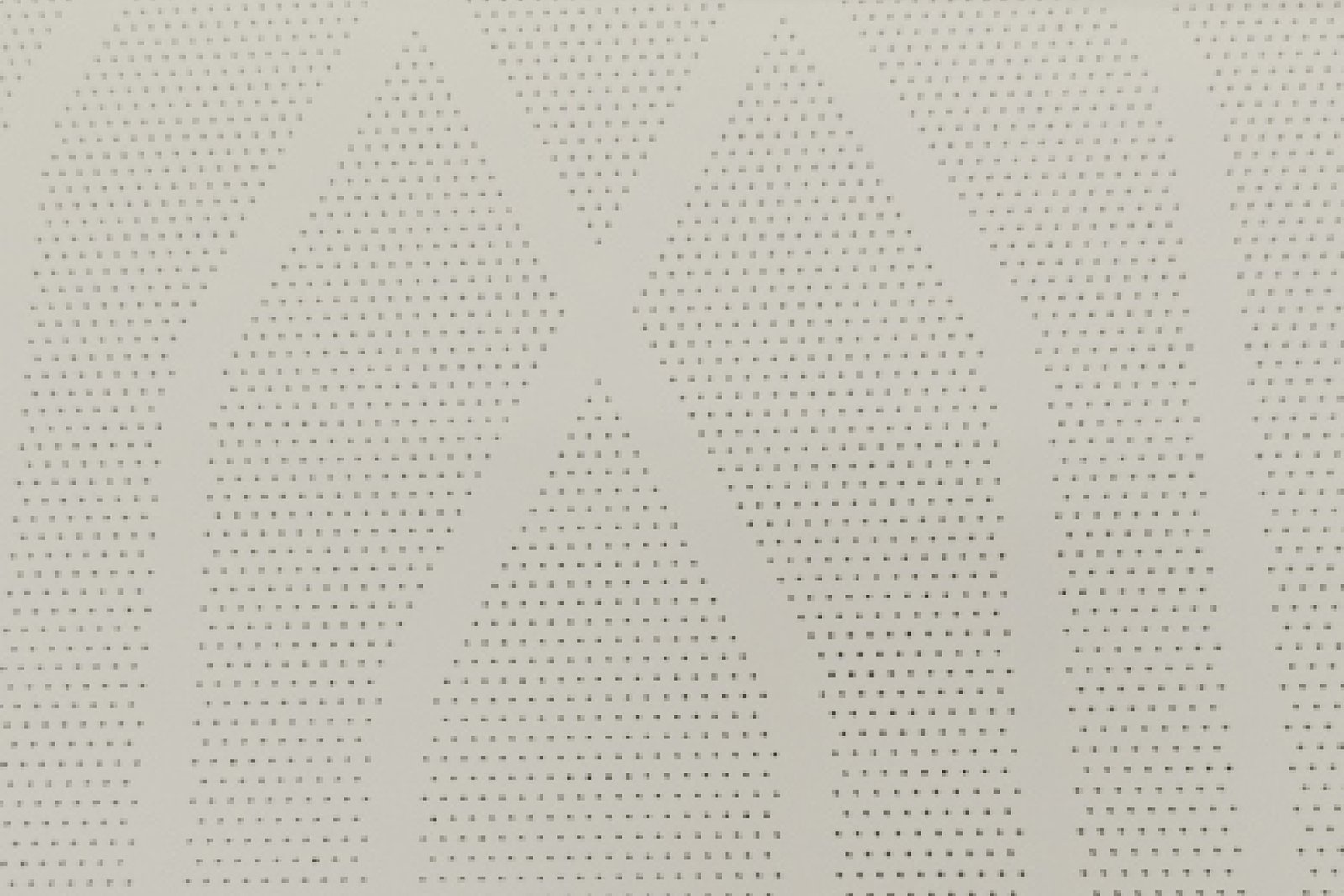
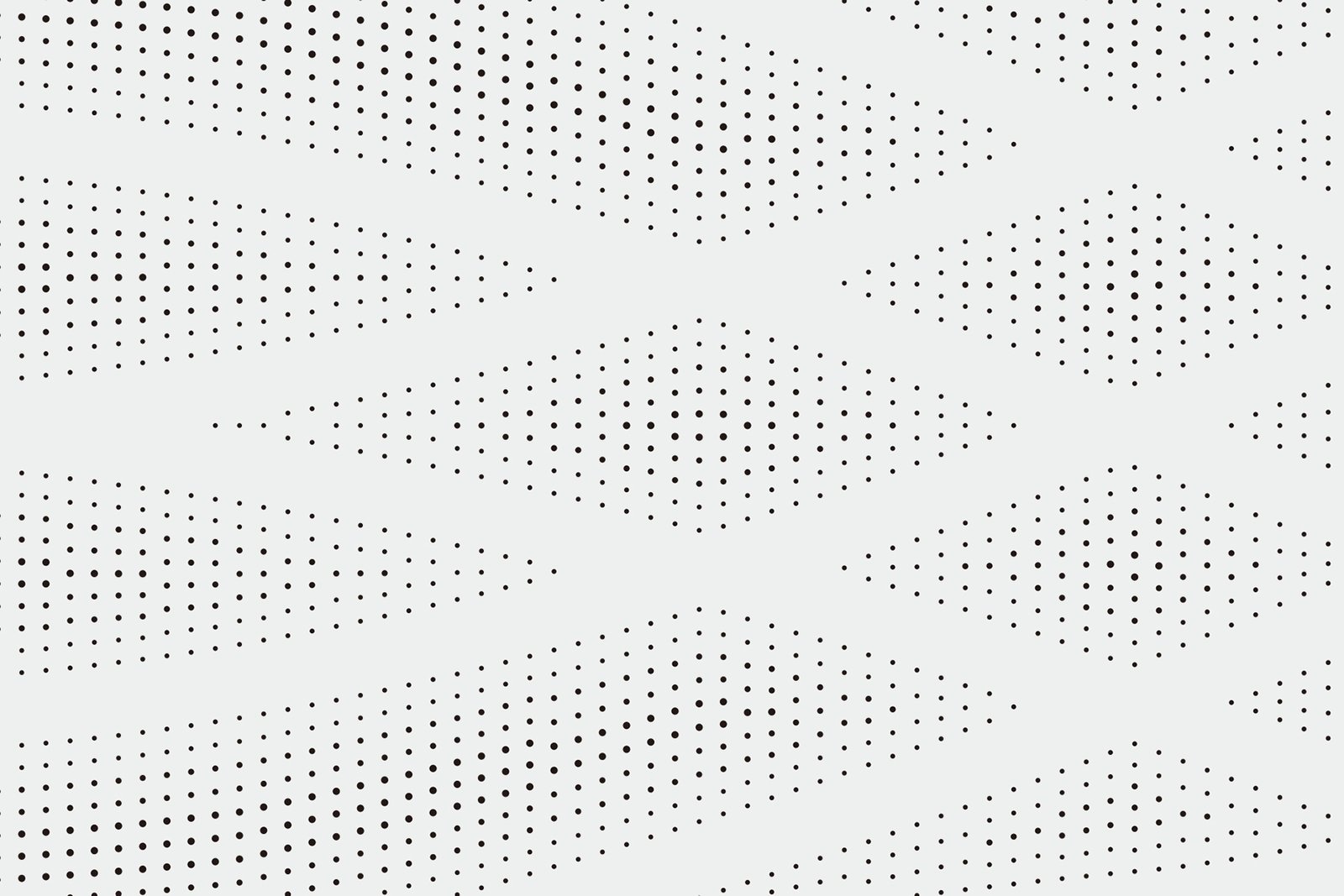
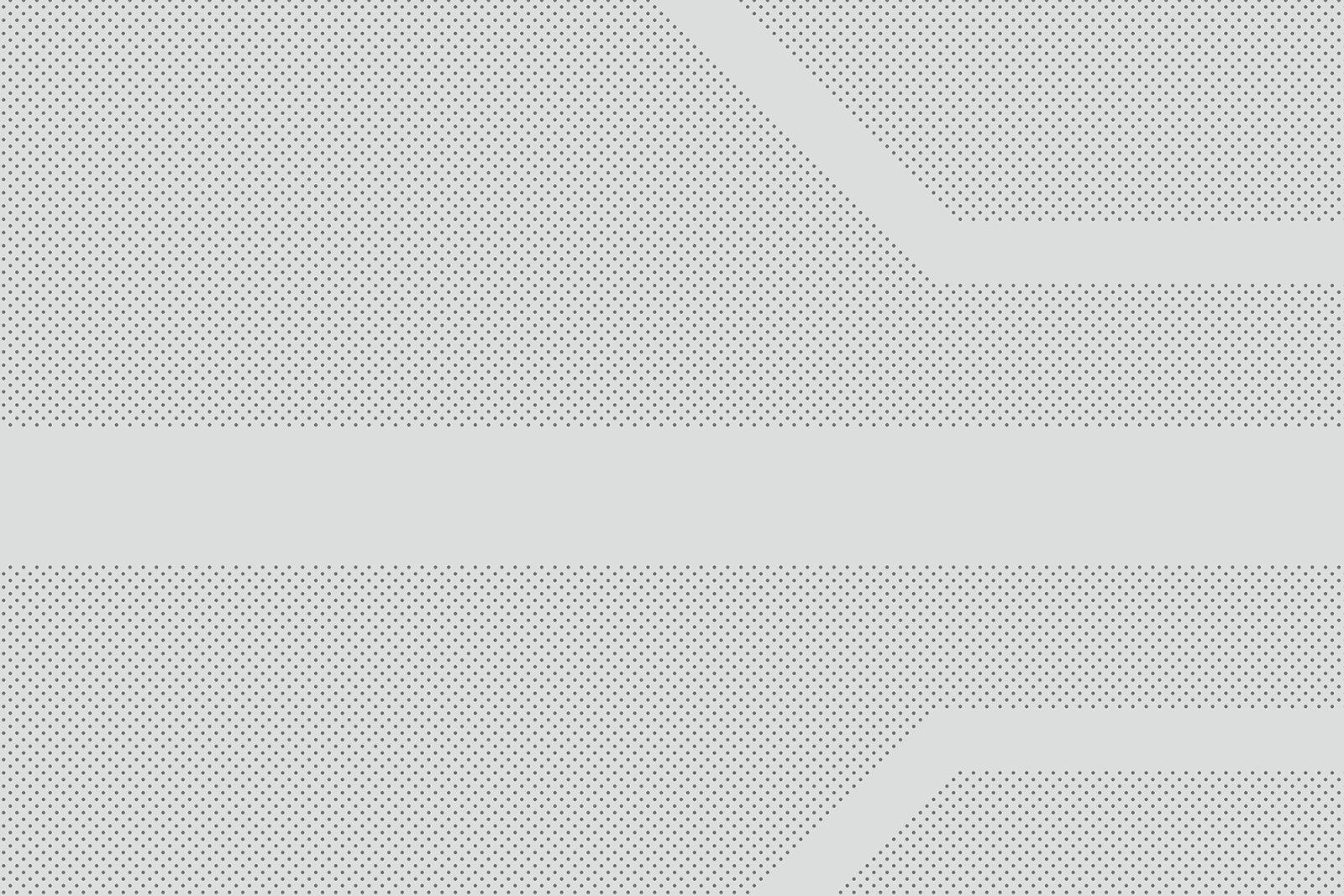
Scope of application
Laser leather perforation machine:
Suitable for leather processing of various thicknesses and materials, especially good at processing fine and complex patterns and hole layouts. Due to the non-contact nature of laser processing, it is particularly suitable for occasions that require high leather surface quality.
CNC leather perforation machine:
Suitable for large-volume, standardized leather punching operations. Since the cost of molds is high and it takes a certain amount of time to replace molds, CNC punching machines are more suitable for producing products with large batches and relatively fixed hole shapes.
cost and efficiency
Laser leather perforation machine:
The initial investment is high, but the laser processing speed is fast and efficient, and there is no need to change molds frequently, so it has a cost advantage in long-term production. In addition, laser processing is easy to automate and integrate, helping to improve production efficiency and flexibility.
CNC leather perforation machine:
The mold cost is high, and the mold needs to be customized according to different hole shapes and sizes, which increases the production cost and cycle. However, once the mold is made, the CNC punching machine can be quickly put into production, suitable for large-volume, standardized production needs.
Summarize
Each has its own advantages
Laser leather perforation machines and CNC leather perforation machines each have their own unique advantages and scope of application. When selecting, comprehensive considerations should be made based on specific production needs, cost budget, and requirements for processing quality and efficiency. For occasions that require high-precision, complex pattern processing and high leather surface quality requirements, laser leather perforation machines may be a better choice; while for large-volume, standardized production needs, CNC leather perforation machines are more economical sex and practicality.
If you want to watch video of leather punching machine,please visit our YOUTUBE CHANEL https://www.youtube.com/@Anze-Perforation-machine
Some models are shipped assembled in the factory. Large equipment is packaged in several parts and an installation manual is provided. All equipment is equipped with user manuals in Chinese and English.
Customers can send someone to anze factory to learn or we send technical experts to provide on-site training
The machine should be fixed on a stable table and the environment should be kept clean and tidy to avoid contact with dust, static electricity, humidity, and chips to cause parts failure.
We have an experienced after-sales team 24h online service and a completafter-sale system. Factory trainning support, Video technical available to service machinery overseas. support, online support, Engineers.
Of course we do welcome to visiting our company and have a face-to-face communication to advance mutual business.
Lead time varies depending on the order quantity and customization, typically ranging from 7 to 10 working days.If it is a custom leather punching machine order, it takes 1-2 months.