Last Updated on 2025-04-19 by Anze
Leather has been a cornerstone of human craftsmanship for millennia, serving as a durable and versatile material for clothing, footwear, furniture, and automotive interiors. Central to transforming raw leather into functional and decorative products is the process of perforation—creating precise holes or patterns to enhance aesthetics, ventilation, and usability. Over centuries, leather perforating tools have evolved dramatically, reflecting advancements in technology, materials, and industrial demands. As a leading leather perforating machine manufacturer, we explore this fascinating journey to highlight how innovation has reshaped the industry and positioned modern tools as indispensable assets in today’s manufacturing landscape.
1. Early Beginnings: Manual leather perforating Tools and Artisanal Mastery
The origins of leather perforation trace back to ancient civilizations, where artisans relied on rudimentary tools to craft functional and ornamental designs. Early leather perforating tools included:
- Awls and Punches: Handheld tools made from bone, stone, or metal, used to pierce holes for stitching or decorative patterns.
- Stamps and Dies: Carved wooden or metal stamps pressed into leather to create repetitive motifs.
These tools required immense skill and time, limiting production to small-scale, bespoke items. While effective for their era, manual methods struggled to meet growing demands for consistency and speed.
2. The Industrial Revolution: Mechanization Takes Hold
The 18th and 19th centuries marked a turning point with the advent of mechanization. Innovations like the fly press and mechanical punch machines revolutionized leatherworking:
- Fly Presses: Lever-operated machines that applied uniform pressure to metal dies, enabling faster and more consistent hole punching.
- Roller Perforators: Machines with rotating cylinders fitted with spikes, used to create evenly spaced holes in leather belts or straps.
These advancements allowed for mass production, particularly in footwear and saddlery industries. However, early machines were still limited in precision and required significant manual intervention.
3. The 20th Century: leather perforating tools mechanization
The rise of automotive and furniture industries in the 20th century demanded higher precision and customization in leather perforation. Key developments included:
- Hydraulic and Pneumatic Presses: These machines used pressurized systems to drive punches, offering greater force and control.
- Interchangeable Dies: Standardized die sets enabled manufacturers to switch between hole patterns quickly, catering to diverse product requirements.
- Conveyor-Belt Systems: Integrated workflows allowed semi-automated processing of large leather sheets.
This era also saw the emergence of die-cutting machines, which combined perforation with cutting to streamline production of complex shapes like car seat covers or handbag panels.
4. The Digital Age: Automation and Computer-Aided Design improve performance of leather perforating tools
The late 20th and early 21st centuries brought transformative technologies that redefined leather perforating tools:
a. CNC (Computer Numerical Control) Machines
CNC technology enabled programmable control over perforation patterns. Operators could input designs via software, allowing for intricate geometries and repeatable accuracy. This was a game-changer for industries like automotive interiors, where custom perforation patterns became a signature of luxury brands.
b. Laser Perforation
Laser technology introduced a non-contact method of perforation. High-powered lasers vaporized leather fibers to create micro-holes with unmatched precision. Benefits included:
- No Physical Wear: Unlike mechanical punches, lasers eliminated tool degradation.
- Complex Designs: Capable of producing gradients, logos, and variable-density patterns.
- Material Versatility: Suitable for delicate or synthetic leathers.
However, laser systems initially faced challenges with speed and cost, limiting their adoption to high-end applications.
c. Servo-Electric Punching Machines
Modern servo-electric systems combined the speed of hydraulic presses with the precision of CNC controls. Features like automatic tool changers, real-time monitoring, and IoT connectivity made these machines ideal for high-volume, high-mix production.

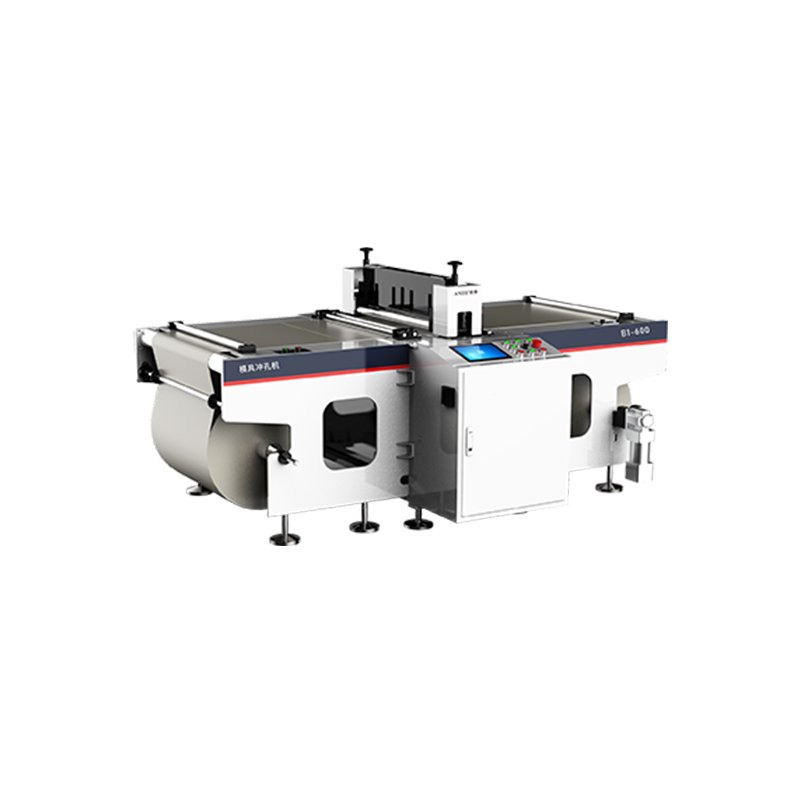
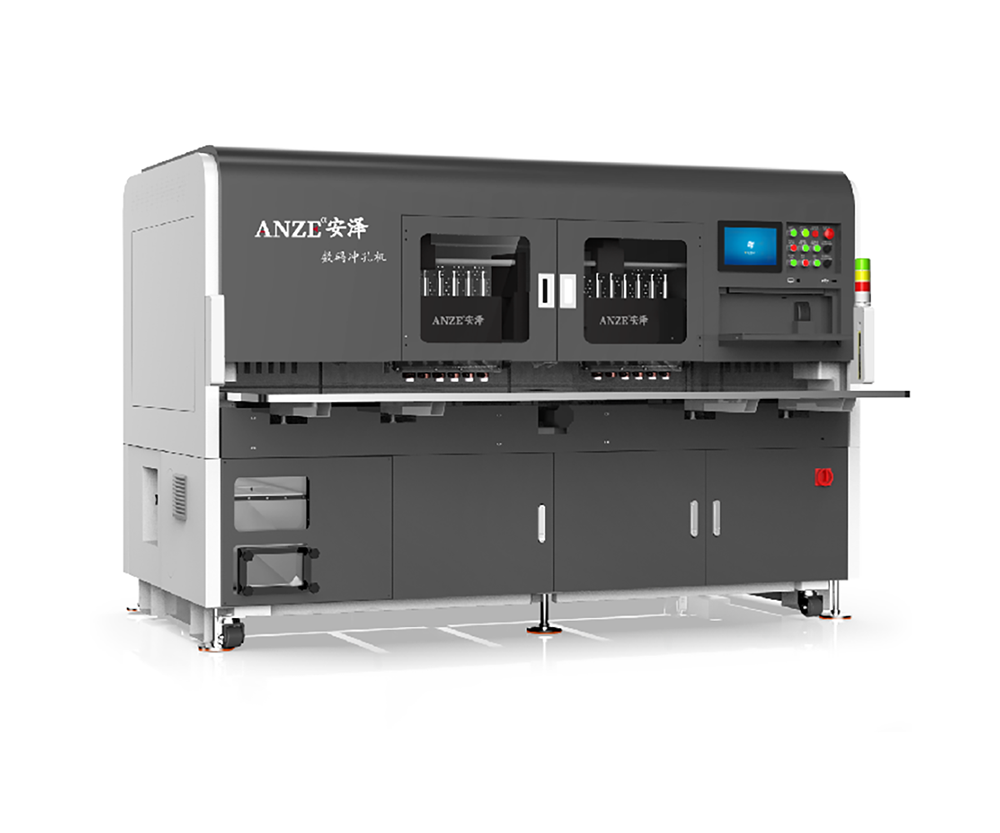
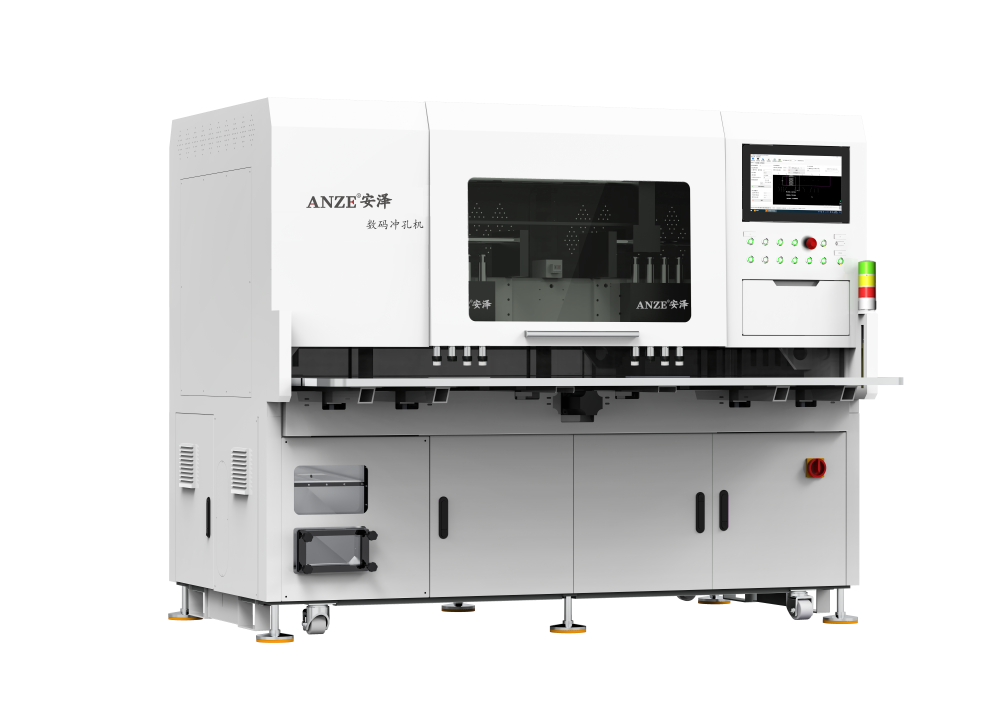
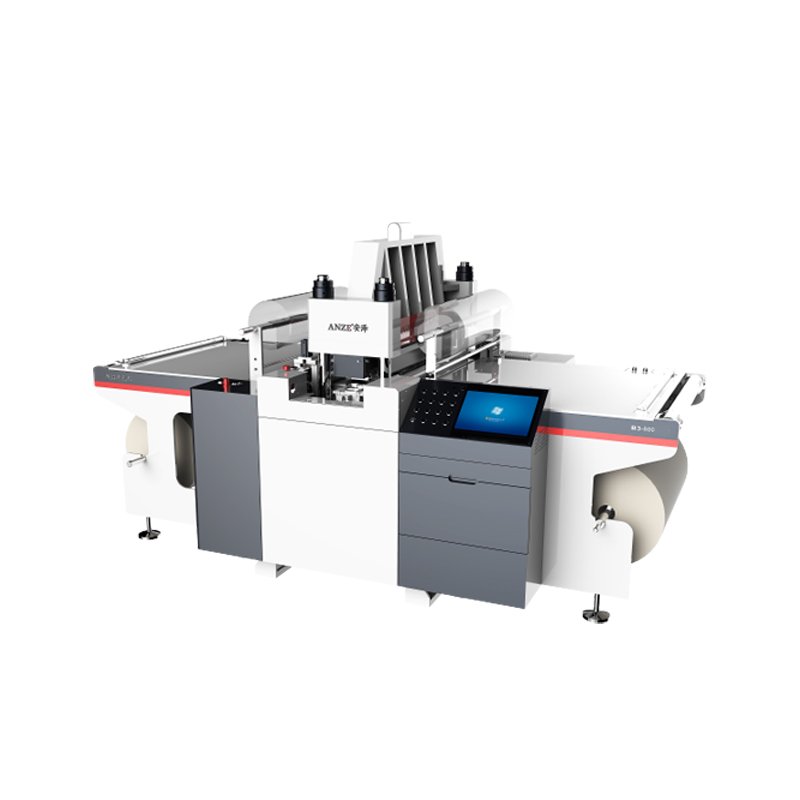
5. Modern Innovations: Smart and Sustainable Solutions
Today’s leather perforating tools are defined by intelligence, efficiency, and sustainability—priorities driven by Industry 4.0 and environmental regulations. Key trends include:
a. AI-Driven Optimization
Advanced algorithms analyze leather grain, thickness, and defects to optimize punching paths, minimizing waste and maximizing yield. AI also predicts maintenance needs, reducing downtime.
b. Hybrid Systems
Combining laser and mechanical punching in a single machine offers flexibility. For example, a hybrid tool might use lasers for fine details and mechanical punches for high-speed bulk processing.
c. Eco-Conscious Design
- Energy Efficiency: Machines with regenerative drives and low-power modes reduce energy consumption.
- Recyclable Components: Modular designs allow easy replacement of parts, extending machine lifespan.
- Waste Reduction: Precision tooling and nesting software ensure minimal leather scrap.
d. Customization at Scale
Digital workflows enable mass customization. A car seat manufacturer, for instance, can produce thousands of seat covers with unique perforation patterns tailored to individual customer preferences—all without slowing production.
6. The Role of a Modern Leather Perforating Machine Manufacturer
As a leather perforating machine manufacturer, our mission is to bridge historical craftsmanship with cutting-edge technology. Here’s how we contribute to this evolution:
a. Advanced Machine Lineup
Our product portfolio includes:
- Multi-Axis CNC Punching Machines: For automotive and aerospace-grade leather.
- Laser-Perforation Systems: Ideal for luxury goods and intricate designs.
- High-Speed Servo Presses: Built for large-scale industrial applications.
b. Smart Factory Integration
Our machines support IoT connectivity, enabling seamless integration into smart factories. Real-time data analytics help clients monitor efficiency, predict failures, and optimize workflows.
c. Sustainability Commitments
We design machines that align with circular economy principles, from energy-efficient operations to compatibility with recycled leathers.
d. Global Support and Training
Beyond hardware, we provide software suites for design simulation and remote troubleshooting, ensuring clients maximize their investment.
7. Future Trends: What Lies Ahead?
The evolution of leather perforating tools is far from over. Emerging trends include:
- Nanotechnology: Ultra-fine perforation for breathable yet durable medical or athletic leathers.
- 3D-Printed Tools: Custom dies and punches produced on-demand via additive manufacturing.
- Biodegradable Leathers: Machines adapted to handle eco-friendly materials without compromising performance.
Precision Meets Progress
From ancient awls to AI-powered systems, leather perforating tools have undergone a remarkable transformation. Each era’s innovations addressed the limitations of its predecessors, unlocking new possibilities in design, efficiency, and sustainability. As a forward-thinking leather perforating machine manufacturer, we take pride in driving this evolution, equipping our clients with tools that turn creative visions into tangible, high-quality products.
Whether crafting the plush interiors of a luxury car or the intricate details of a designer handbag, modern perforation technology ensures that leather remains not just a material, but a canvas for innovation. Join us in shaping the future—one precise perforation at a time.
Explore our range of state-of-the-art leather perforating machines and discover how we’re redefining the art of leather craftsmanship.
Some models are shipped assembled in the factory. Large equipment is packaged in several parts and an installation manual is provided. All equipment is equipped with user manuals in Chinese and English.
Customers can send someone to anze factory to learn or we send technical experts to provide on-site training
The machine should be fixed on a stable table and the environment should be kept clean and tidy to avoid contact with dust, static electricity, humidity, and chips to cause parts failure.
We have an experienced after-sales team 24h online service and a completafter-sale system. Factory trainning support, Video technical available to service machinery overseas. support, online support, Engineers.
Of course we do welcome to visiting our company and have a face-to-face communication to advance mutual business.
Lead time varies depending on the order quantity and customization, typically ranging from 7 to 10 working days.If it is a custom leather punching machine order, it takes 1-2 months.